What Is Induction Cap Sealing?
Induction cap sealing is a non-contact process by which a seal is bonded to the mouth of a container beneath it’s cap. Induction cap sealing was originally intended to prevent leakage of chemicals from plastic bottles in chemistry labs. Today, this process is used for sealing food and beverage, drugs, cosmetics, chemicals, and more.
The induction cap sealing processes begins by selecting a suitable container. Most container manufacturers will specify which of their containers are designed for induction cap sealing. The container can be made of any non-conductive material such as plastic or glass. It should be ridged, and close with some type cap or lid. The type of seal is chosen based the material of the container, as well as the needs of the manufacturer and customer. Induction cap seals typically consist of a piece of metal foil, usually aluminum, that is cut to fit beneath the cap of a container. This piece of foil is coated with a layer of polymer. A cardboard or Styrofoam liner is usually affixed to the top side of the seal, although liner-less seals are also available. Most of the time, containers specified for induction cap sealing will come with the seal already inserted into the cap. In this case, the container can be filled and caped with conventional filling and caping equipment, or by hand. If it does not have the seal pre-inserted, you will need to insert it by hand, or use an additional machine.
Once the container is filled and caped it can be passed along to the induction cap sealing machine. These machines create an alternating electromagnetic field that interacts with the foil of the seal through the cap of the container causing it to heat up. This heat causes the polymer layer to melt and bond with the lip of the container. When the cap is removed, the foil remains bonded to the lip of the container.

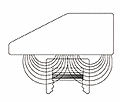
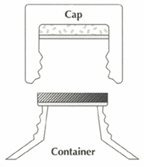